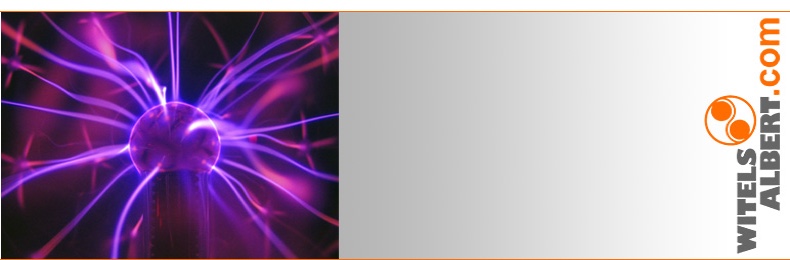
Constantly evolving production environments, greater use of automation, tightly integrated sub-processes, a relentless increase in production speeds, new materials and advanced business strategies have a direct impact on products that are used to straighten, feed, drive and guide process materials.
Our customers have to supply top quality process materials and products to their customers, which can be produced at the lowest possible cost within tight tolerances using a highly stable process.
The mission of WITELS-ALBERT is to design and manufacture products that enable our customers to achieve these goals in the real world environment. HS series high-speed straighteners, PO position counters which ensure defined, reproducible settings of the straightening rolls and the CS semi-automatic wire straightener adjustment system which provides continuous product and process data are just a few examples of our extensive product portfolio and the wide range of technical features.
In addition to our advanced range of feed, drive, guide and straightener products, WITELS-ALBERT provides a knowledge base as a service which contains a wealth of information about the theoretical and practical aspects of straightening wire and multi-wire process materials. Our customers have free access to this information, and when they combine this knowledge with the right straightening products, they are able to design the best straightening process for the particular application and manage the challenges which arise in the straightening process on the production floor.
We want to use our expertise to help ensure that the straightening process is treated as an independent sub-process which is influenced by upstream and downstream processes. In our view, pay-off from a reel and feeding wire past a guide roll are sub-processes which can have a positive or negative impact on the subsequent straightening process. There are process interfaces at the feed and delivery points of a straightening unit or system, and the interface parameters can be objectively identified. There is no doubt that the quality of the finished product depends on the consistency of these parameters.
Take inspiration from our knowledge of the straightening process and benefit from our expertise. Browse through our knowledge base and learn about the factors which determine the number of straightening rolls you need or find out more about the drive force that is needed for straightening, the perfect combination of straighteners and straightening systems, how to handle a killing unit, simulation of wire straightening, automation of the wire straightening process, the service life of straightening rolls, initial curvature, straightening planes, the zero line, adjustment of the straightening rolls, etc.
The Guideline (in progress, issue 03. 04. 2019)